Dust Monitoring can help you manage your dust problems before they become severe and costly, improve team member comfort and reduce the risk of future respiratory illnesses such as asthma or chronic obstructive pulmonary disease (COPD). Real-time dust monitors provide real-time data regarding your facility’s particulate matter levels. They can help you keep your facility at an acceptable dust level, preventing team member discomfort and illness.
Cheap To Set Up
Dust monitors are quick and simple instead of running to work with a runny nose or watering eyes. You can go about your day at work without worrying about what’s in the air you breathe. Dust monitors collect data on temperature, humidity, carbon dioxide levels, and dust particulates in your air. That means you get real-time reports on whether it’s safe to breathe or if there is too much dust in your air that day. These devices are small enough that you can set them up at work or school without impacting your daily routine. If things get too smoky for comfort, you’ll know when to take action to fix it before it affects anyone else.
Quick And Simple
The whole process should be quick and straightforward, with no fuss involved. Just place your order online, receive it via UPS, plug it in, and get to work. Your dust monitor can be used within minutes of opening your package, so you won’t have to spend long hours trying to set it up. Dust monitoring is also inexpensive compared to other air quality systems. You can purchase one without sacrificing performance or quality! If you compare dust monitors to high-end models that are ten times more expensive, you’ll see that they offer comparable features at a fraction of the cost.
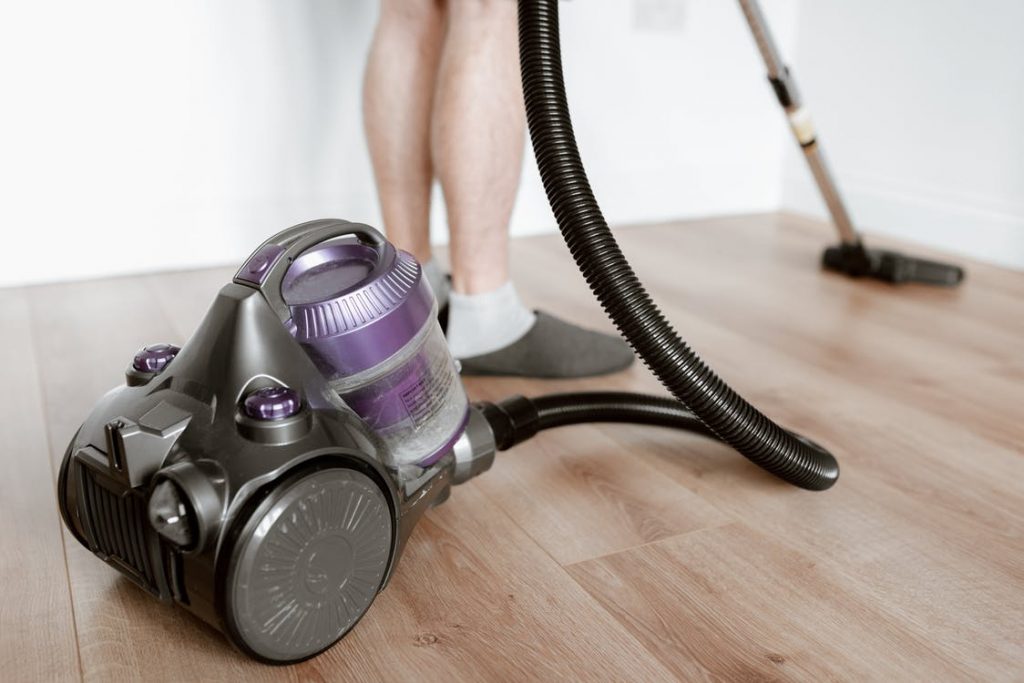
Complaint Management
A powerful advantage to using Real-Time Dust Monitors is that they provide an excellent way to manage complaints. Not only do Real-Time Dust Monitors allow you to monitor dust levels in your facility, but they can also help identify if any employees are not following protocol or procedure. This is because Real-Time Dust Monitors have two main components: 1) a real-time pollution sensor and 2) a data logger. The data logger records temperature, pressure, humidity, vibration, etc., all of which are sent to a server for analysis. If there are any discrepancies or issues with your dust monitors being tampered with by disgruntled employees—the data logger will alert management immediately! This gives you vital information on how employee behaviour is affecting your environment—leading to improved morale and productivity.
Review Of Mitigation Measures
Every dust monitoring technology has its pluses and minuses, but it’s critical to perform a comprehensive review of mitigation measure effectiveness. If you can’t provide data that proves that your dust monitors keep workers safe—especially if OSHA or other governmental agencies are breathing down your neck—you need to figure out where things went wrong and immediately implement fixes. Also, be sure to report any findings regarding worker safety issues to OSHA, so they don’t find out on their own. It might cost you time and money, but it could also keep you from losing an employee or even saving a life.
Identify The Occurrence Of Dust Events
Just because there is no immediate discomfort or adverse health effects doesn’t mean that dust events don’t occur. Dust monitoring can help identify when they do happen. As noted above, short-term exposure to dust levels that are considered safe by regulatory agencies may still cause adverse effects when employees work in areas with higher than normal exposures. By identifying these occasions through monitoring, employers can work proactively to reduce employee exposure during those periods.